Project: New Kattwyk Bridge, Hamburg (Germany).
Solutions provided: Insulating Cable Ladder 67 and Insulating Cable Tray 66.
Completion year: 2020.
The Hamburg harbour is the first harbour in Germany, the third in Europe and one of the first in the world in terms of container traffic. To establish itself as an industrial hub, it needed a new generation bridge dedicated exclusively to rail transport.
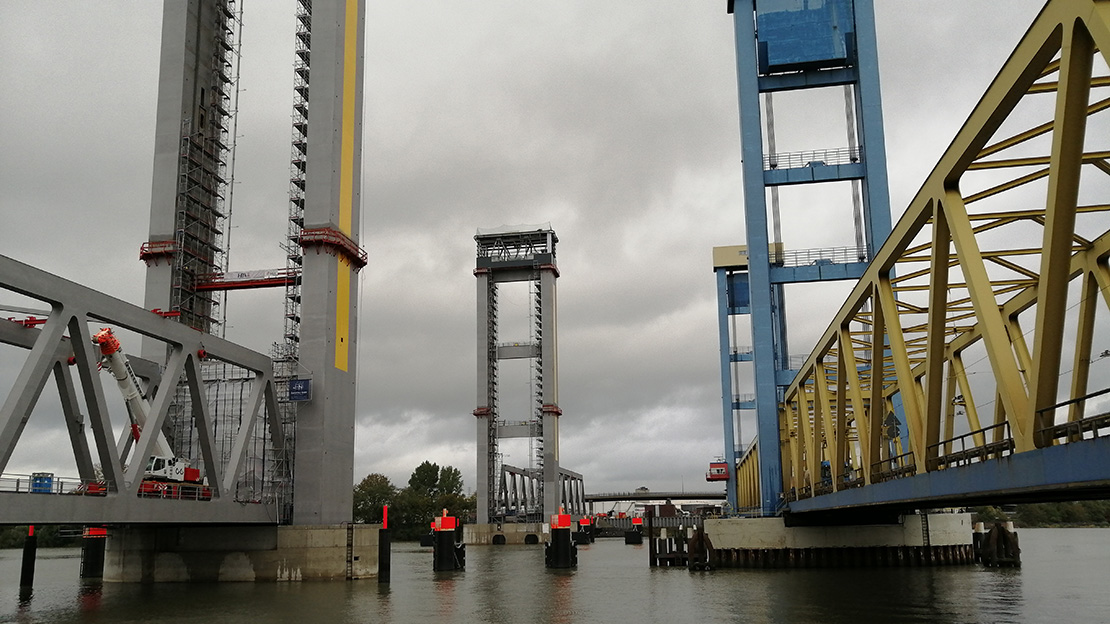
The new Kattwyk Bridge, Europe's largest drawbridge, stands out in plain sight, but all its control and safety mechanisms are not visible, as they run under the river Elbe, through a service gallery where the cables run.
The challenge: to implement, in a mega-project defined to the last detail and in the middle of the execution phase, a cable conduction system different from the initial one and unknown to the owner.
The challenge of adapting to a pre-established context
We had to adapt to the existing construction specifications and to fix the profiles and the cable trays at the predetermined points, without being able to make any modifications due to the impossibility of drilling into the concrete.
All this in a narrow concrete gallery with an inside diameter of 2m, 35m deep and 122m long.
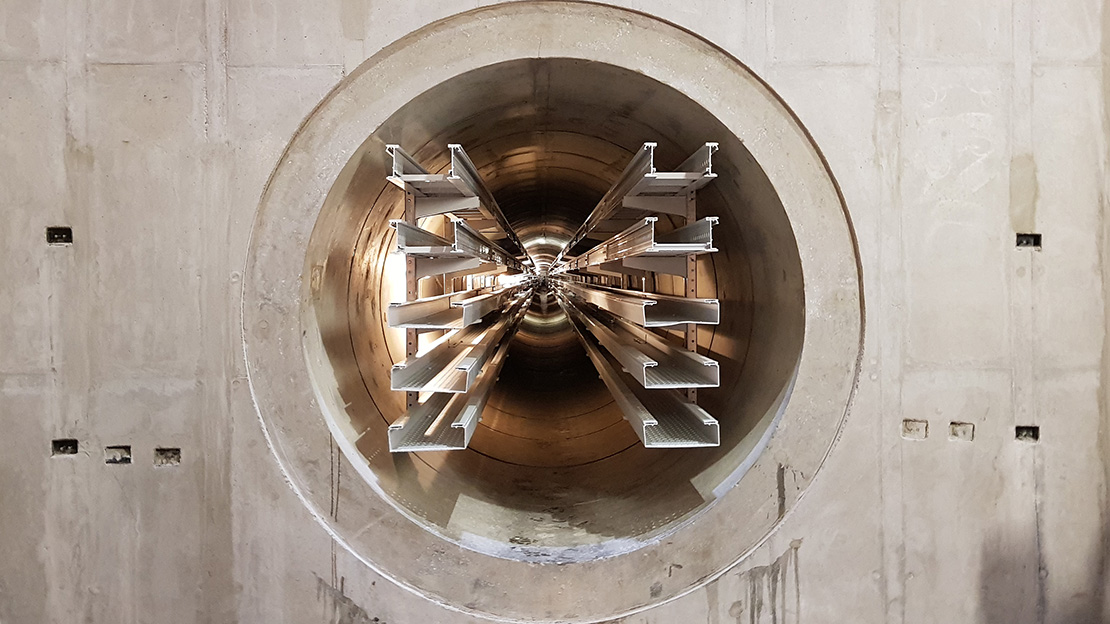
The cabling that runs through the tunnel serves to power and control the lifting system of the railway structure, as well as the safety and signalling systems (barriers and traffic lights). In addition, there are the cables for the gallery itself: internal lighting and emergency and safety lights.
The requirements of this installation were clear, but mechanically it was difficult to meet them:
- From each side of the 2m diameter tunnel, cables of different tensions had to be passed through, leaving enough space in the central axis of the gallery for the operators to pass through and work safely.
- Fixing the trays only on the wall side. In this way, easier access was achieved for handling the cabling for inspections, maintenance operations, etc.).
- Respecting the predetermined distance of the supports.
- The cable anchoring system had to be compatible with the existing rails.
- Separation of circuits on 5 levels on both sides of the gallery: 3 for signal and 2 for medium voltage.
- To support the load of the cables already defined.
- Minimum maintenance.
To all this, other characteristics are added: electrically insulating materials to avoid equipotentiality problems, that offer electrical safety against indirect contacts and that are resistant to corrosion and to the damp and cold environments of an underground gallery.
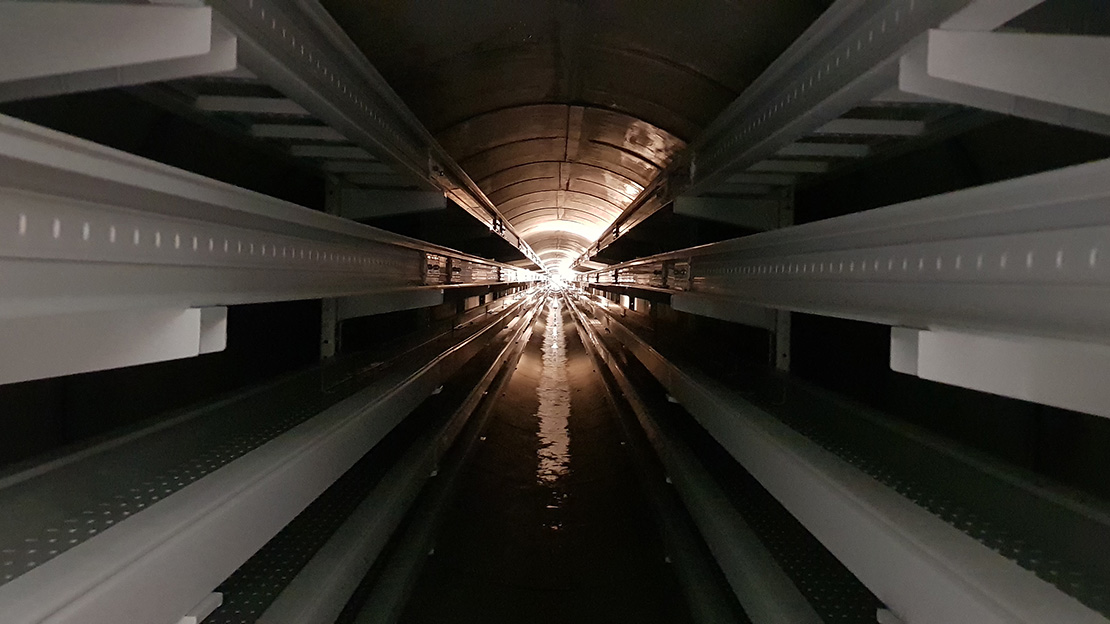
Operational safety, making the tunnel work and minimising electrical failures was another essential requirement.
¨It is important that such a bridge can be optimally controlled [...] the power and data cables that are distributed through the tunnel are very, very important to be able to manoeuvre this bridge later on" (Jens Meier, Managing Director HPA).
The immediate availability of the material, since the construction site was already underway, was also decisive in the final decision.
In the following article, we will tell you about the solution we offered to meet all the needs of this mega project.