Suggested solution: Insulating cable tray 66, Omega profile and Joint cover piece in thermoplastic material.
Project finished: July 2014
The Spanish railway industry is making huge steps in the implementation of automatic trains using remote control. 25% of Barcelona’s metro network runs driver-free. This is the result of a gradual transformation process including the construction of new automatic underground rail lines like Barcelona’s pioneering remote L9/10 which is a reference in innovative European infrastructures.
The technology in remote control system
Every day, more and more urban rail lines are automated, making them more efficient, safe and environmentally friendly. This is made possible thanks to advanced remote control technology in every part of the system which allows distance control over all the systems and resources involved in these trains. By remote control, these lines operate without personnel on board at the rated speed and stopping at stations according to the programmed instructions.
The project
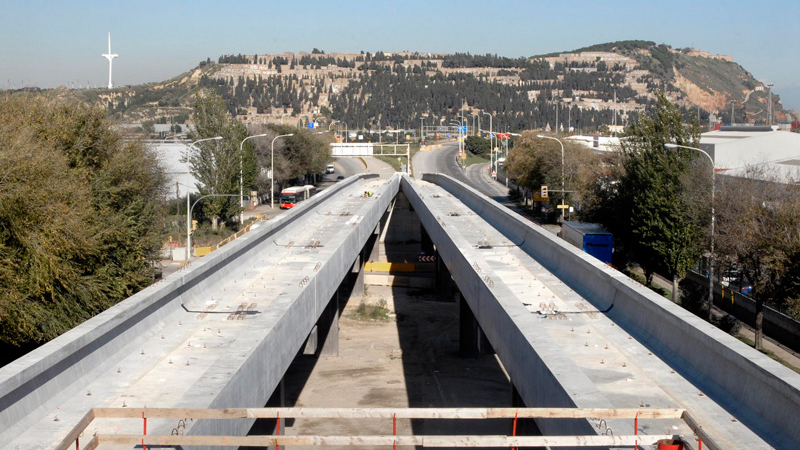
In 2011 Unex visited the L9/10 metro line for the first time. It has a total length of 47.8 km (43.71 km underground) and 52 stations in five different municipalities of the metropolitan area of Barcelona: Santa Coloma de Gramanet, Badalona, Barcelona, L’Hospitalet de Llobregat and El Prat de Llobregat. The central part of the route is shared between the L9 and L10 lines.
The first installation of the 3 that were approved, is the one that runs through Zona Franca. The brief was the following:
The challenge: Create a cable conduction system to protect the remote control technology that allows the circulation of driver-free trains in a 100% safe, flexible and reliable way.
The solution
A support, fixing and conduction system for the remote-control network made up of more than 20,000 meters of Insulating Cable Tray 66 with cover in thermoplastic material (U23X) sizes 100x200 and 100x300, a galvanized steel Omega profile coated in grey epoxy made to the clients specifications in order to overcome the geometrical variations of the viaduct and the thermoplastic joint covers pieces designed to cover the end cuts of the cable tray and the cable tray cover.
This cable tray system is capable of overcoming the security, corrosion, mechanical and electromagnetic conditions of the area.
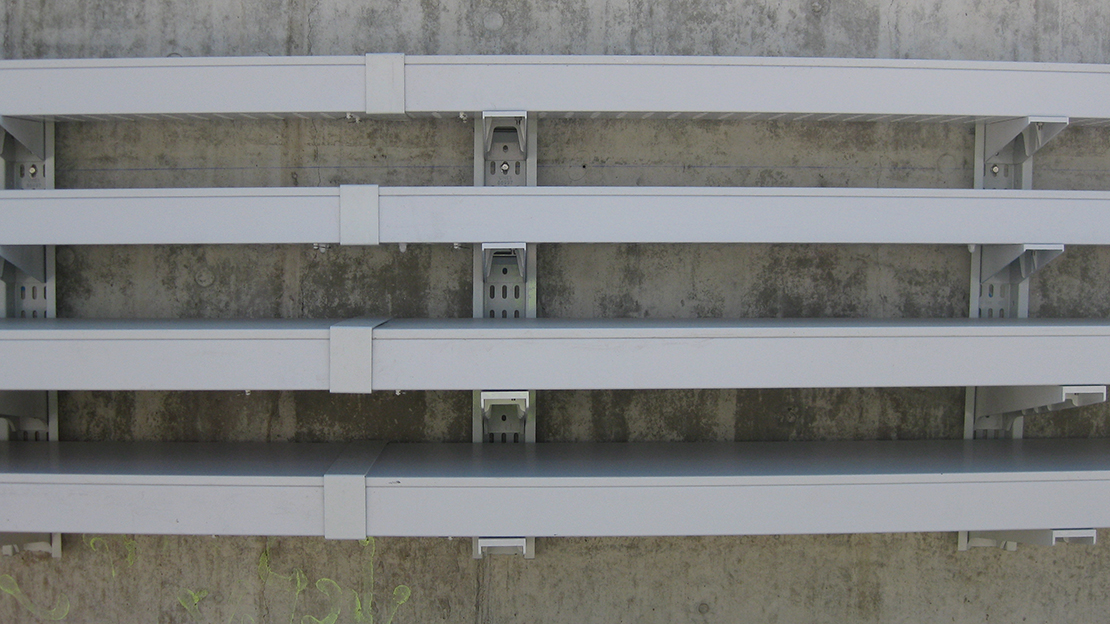
Electrical insulation
The insulating cable tray 66 is made from insulating material, an own formulated raw material, and has a high dielectric strength, protecting people from the risk of electrocution through indirect contact
The insulating cable tray 66 is an inert component and avoids overload in the cable network.
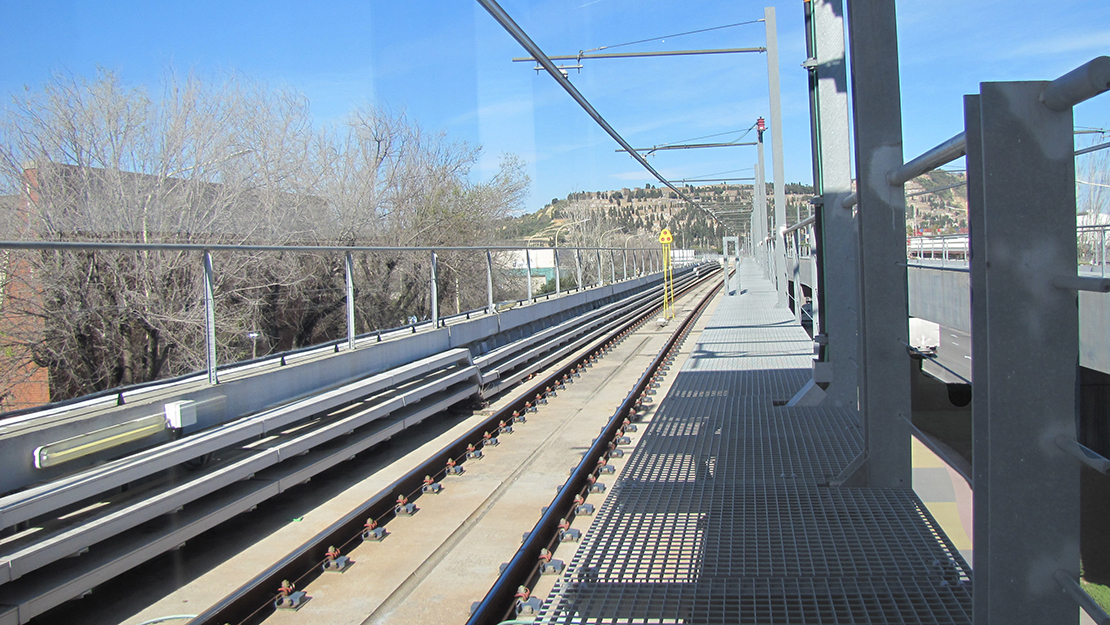
High impact absorption
The thermoplastic material is capable of absorbing shocks. Therefore, it offers better resistance to the train’s vibrations. Unex cable trays are designed to be impact-resistant.
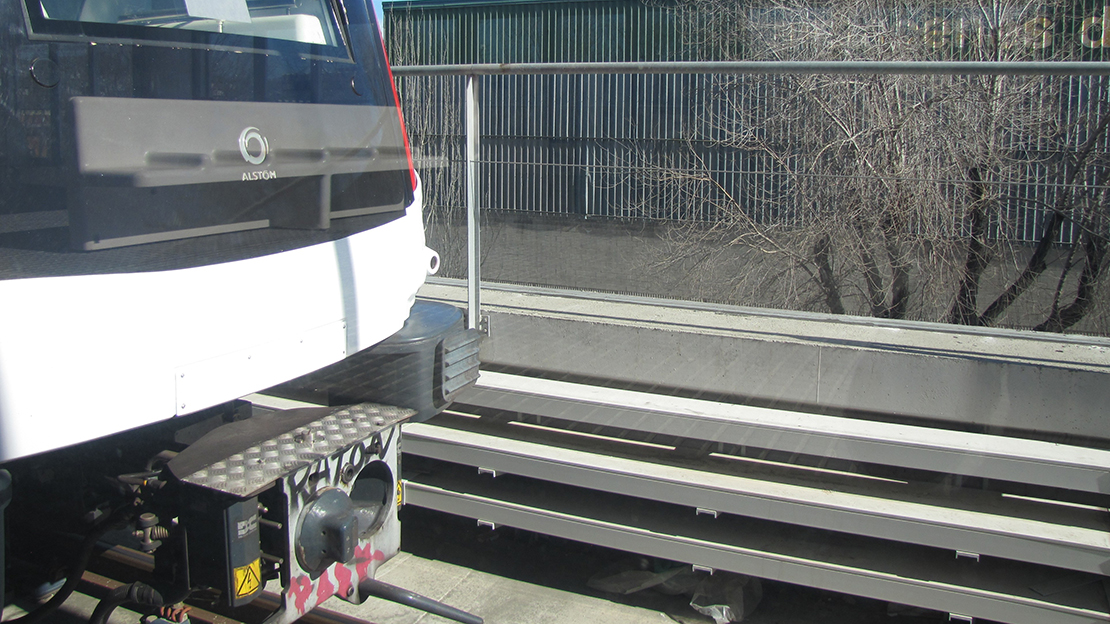
UV rays and saline resistant
The proximity of the viaduct to the sea means the materials used are affected by the levels of ambient salinity of the area. Thanks to Unex’s insulating raw material the cable tray is unalterable against corrosion. According to the Cable tray standard IEC 61537:2007, Unex insulating materials "are inherently resistant to corrosion and do not require testing
More details about the mounting process, challenges and special requirements that our team encountered during the installation of the cable tray system will be explained in next posts.
Do you need technical assistance for your next project?
On the Unex blog, we cover a wide range of topics of interest and share experiences from our clients. We remind you that all legal information and information regarding compliance with applicable regulations can be found on our official website. We invite you to consult it for a more comprehensive and accurate understanding.