Project: Desalination plant in Perth (Australia)
Suggested solution: Insulating cable ladder 67
Project finished: November 2018
The Kwinana desalination plant, located 25 km south of Perth, is operated by SUEZ and began production in 2006. Today it produces 140 megalitres of fresh drinking water per day, 18% of the total water consumption of Perth, a city of one and a half million inhabitants.
It’s the largest salt water reverse-osmosis (SWRO) plant in Australia and the biggest in the world running on renewable energy. Electricity for the plant is produced in the Emu Downs wind farm, 200km north of Perth, in the Cervantes region, which has 48 turbines and an output of 80 MW.
The Challenge: to provide a cable conduction and protection system for large-calibre power cables specifically conceived to resist the local environmental conditions (UV levels in Australia are among the highest in the world) and corrosion damage caused by water, a phenomenon enhanced by the environmental salinity of the zone.
The substitution of 80 meters of metallic systems was completed in November 2018 with a highly innovative and pioneering system new to the market: the Insulating Cable Ladder 67, the first cable ladder produced in recyclable thermoplastic material. This solution is specially designed for industrial installations and presently coexists with our Insulating Cable Tray 66, which was previously installed.
Unalterable against corrosion
The plant, located at Kwinana, treats water from the nearby Cockburn Sound and is exposed to high levels of salinity, a condition that accelerates the corrosion of the installed materials.
Therefore, it was required a material that was able to withstand aggressive environmental conditions. When the Cable Ladder 67 was presented, the client agreed on the convenience of this solution for this installation.
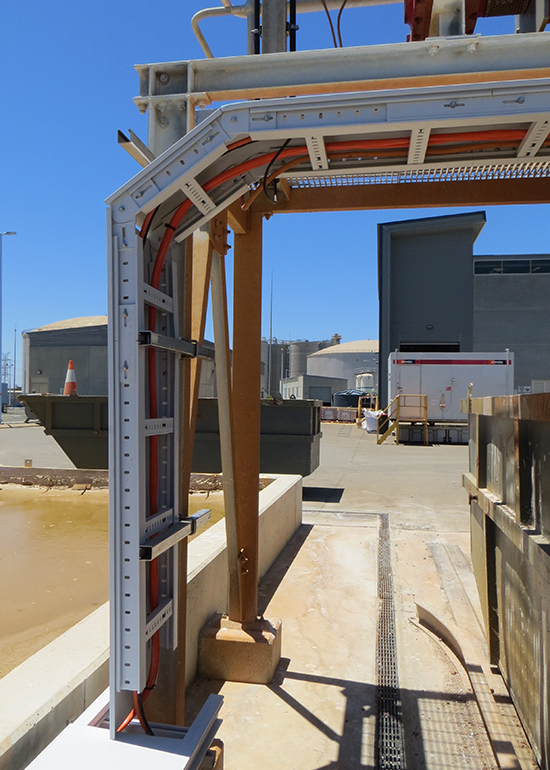
The raw material of the Insulating Cable Ladder 67 and its accessories assures an excellent behaviour in front of humid and saline corrosion as well as in chemical environments.
According to the Cable tray standard IEC 61537:2007, Unex insulating materials "are inherently resistant to corrosion and do not require testing".
Our raw material does not require coating to the final product. Thus, the corrosion protection remains unchanged in the course of time and after cutting and manual processing the material in the worksite.
Good performance outdoors and with exposure to UV rays
Australia has the highest levels of UV radiation on the planet because of its proximity to the equator and its long sunny days, making necessary the use of materials conceived to resist these environmental conditions.
Our raw material is designed to perform well outdoors and resist exposure to UV rays. These properties are backed up by more than 40 years of experience in outdoor installations with the Cable Tray 66.
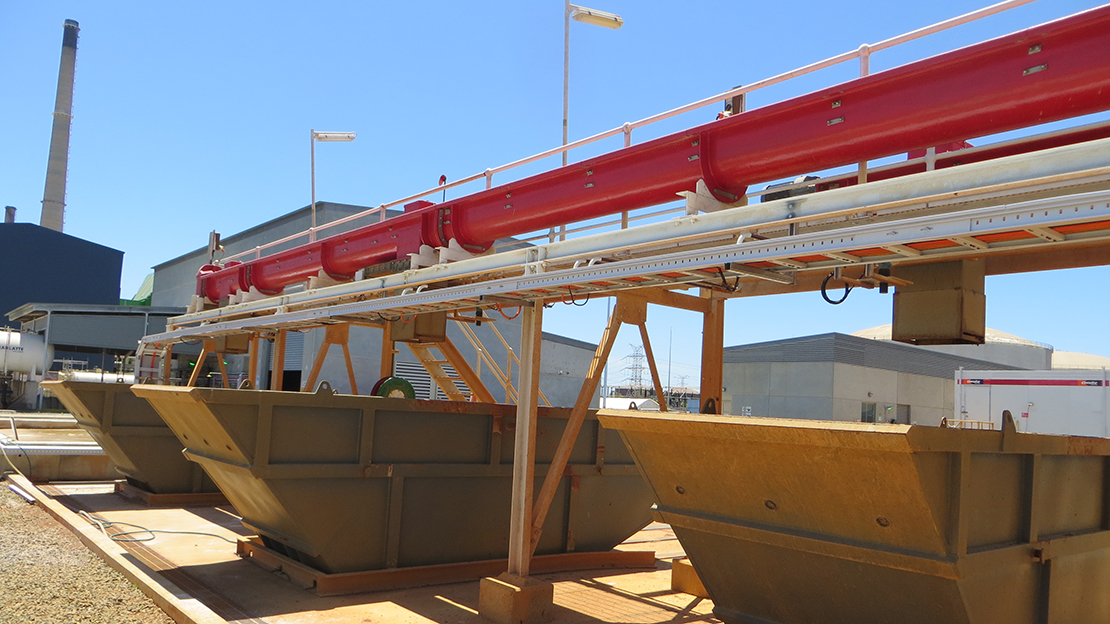
Easy to install
A key characteristic of Unex products is the ease of mounting. Unex offers a complete system of elements to facilitate the installation of the Cable Ladder 67 on site:
- We have designed a kit type system which greatly simplifies the assembly of the cable ladder.
- Form elements ready to mount. The junctions are available in 2 standard bending radii: 300 and 600 mm.
Find out all the details:
Costs and mounting time are reduced
Due to the insulating properties of the product, costs and mounting time are reduced:
- Cutting and manipulation of our material does not produce burrs, sparks or irritating dust. There are no burrs affecting the insulation of the cable system.
- Earthing and coating of the final product is not required, which allows to save in complex tools and reduce mounting and maintenance time.
- Welding for the installation is not needed, therefore mounting time is reduced and the durability of the tools is increased.
Furthermore, the type of material and design of the products allow to reduce the number of operators required to move and mount the pieces. In the Perth desalination plant, the installation of 80 m of cable ladder was completed within a couple of days and a reduced team of operators.
Availability and reliable delivery
The availability and reliability of our deliveries are assured by a complete stock of all our references. Our in-house production capacity allow us to control every stage of the manufacturing process: creation of our own-formulated raw material, product design, quality, packaging, and finally distribution.
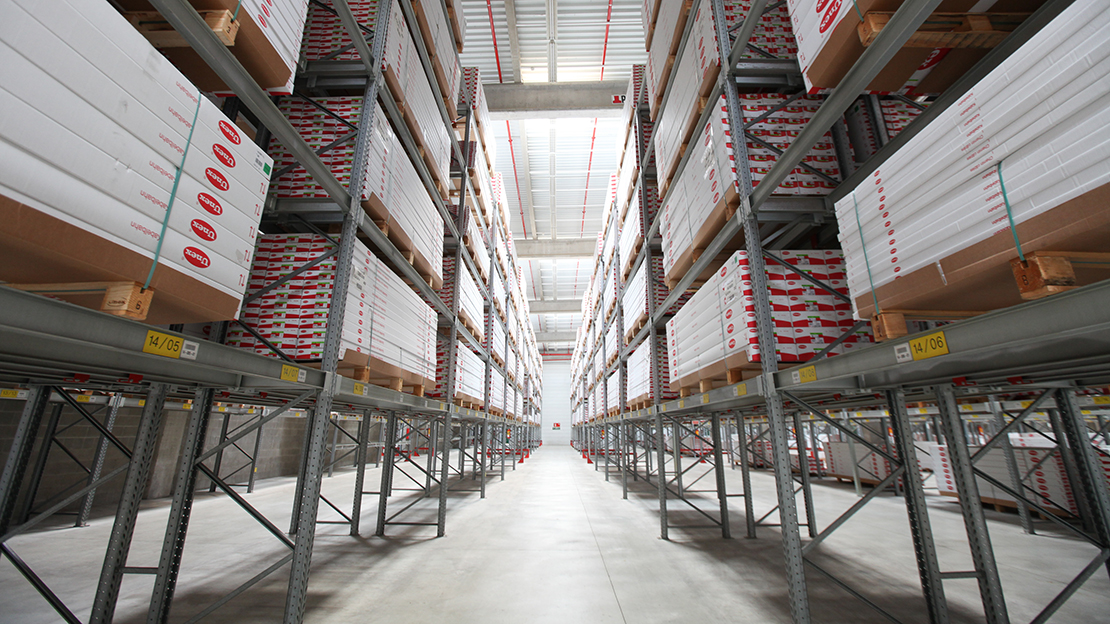
Customer service
At Unex we stand out for offering personalised technical assistance through our in-house team of engineers. By means of personal visits before, during and after the installation we can assess the specific needs of every client, offer the solutions that best suits their needs and tailor them according to the requirements of each installation.
The reliability and quality of our service, quick response and ease of installation along with the quality of our products were key in the success of the Perth project.
Do you need technical assistance for your next project?